In the surface treatment process, the pretreatment is a crucial phase to obtain a high-quality finish, both from aesthetic and functional point of view. Preparing surfaces in a proper way before applying paints and coatings is essential to remove impurities, residues and contaminants that could compromise the final result. The pretreatment not only ensures an impeccable aesthetic result, but also improves the durability and resistance of the finished product.
Why pretreatment is essential to obtain a high-quality finish?
Pretreatment is a crucial phase that has a decisive influence on the quality and durability of the product’s surface finish. In many industries, where materials have to deal extreme conditions, an accurate pretreatment becomes essential to ensure effective protection. Untreated or poorly prepared surfaces may be subject to corrosion, aesthetic degradation, and premature coating failure, leading to increased maintenance and replacement costs.
An effective pretreatment prepares the surface by removing all types of impurities, such as oils, grease, residues, and dust, which can compromise the adhesion of the coating to be applied in subsequent stages. This process is crucial not only to prevent aesthetic defects, such as blisters, cracks, and flaking in the finish, but also to improve the product’s functional performance and durability. For example, a well-pretreated surface is more resistant to chemicals, corrosion, weathering, abrasion, and mechanical stress, thus ensuring long-term protection.
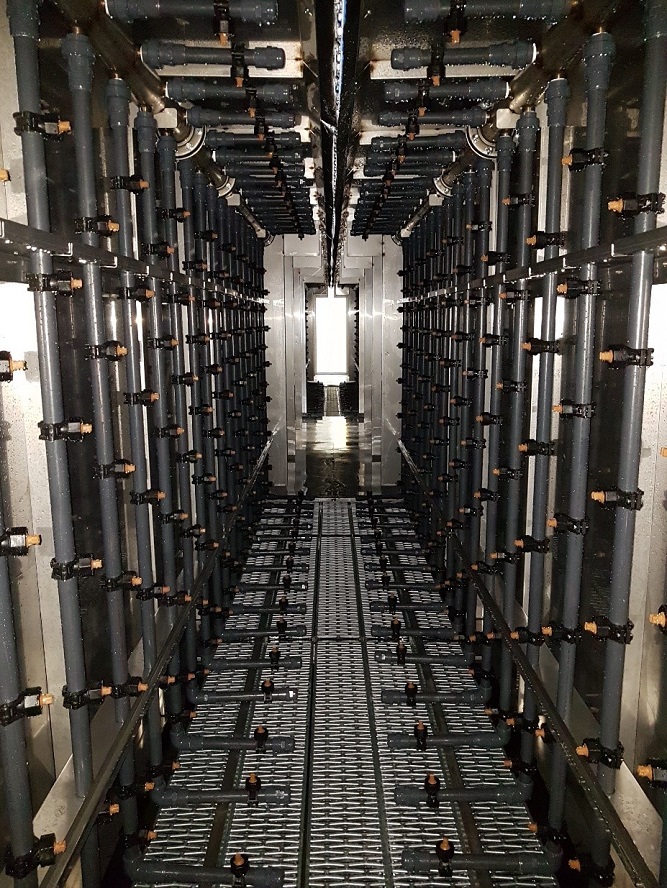
Furthermore, in a more competitive global market context, a high-quality pretreatment allows companies to reduce operating costs and those related to possible reworking of parts, production defects as well as to minimize waste, thus increasing efficiency and overall productivity.
Different types of pretreatments
There are different pretreatment methods, each designed to respond to the specific needs of materials to be treated and the type of coating that will be applied subsequently. The choice of the appropriate pretreatment method depends on the type of surface (metal, plastic, glass, etc.) and the environmental conditions to which the finished product will be exposed. Each of these pretreatment processes offers specific benefits and should be chosen based on the needs of the project and the requirements of the finished product. Whether it is to improve corrosion protection or ensure perfect coating adhesion, correct pretreatment is essential to ensure overall production quality.
There are mainly two types of pretreatment:
Mechanical pretreatment:includes physical processes that modify or prepare the surface through the mechanical action, such as:
- Shot blasting: a jet of grit or other abrasive material is used to remove oxides, old paint or impurities from the surface.
- Brushing: a wire brush is used to clean and smooth the surface.
- Polishing:
used to make the surface smoother and more homogeneous.
Chemical pretreatment: it involves the use of chemicals to prepare the surface, improving its adhesion for subsequent treatments. Some examples include:
- Degreasing: this process is used to remove oils, greases, dust and other contaminants from the surface. This is a fundamental preliminary stage, as any surface residues could prevent the paint or coating from adhering properly, compromising the quality of the finished product.
- Pickling: chemical treatment that removes oxides and impurities from metals using strong acids to clean the surface.
- Phosphating: a chemical process that creates a phosphate layer on the surface of metal that improves adhesion of subsequent coatings, such as paint, and provides corrosion protection.
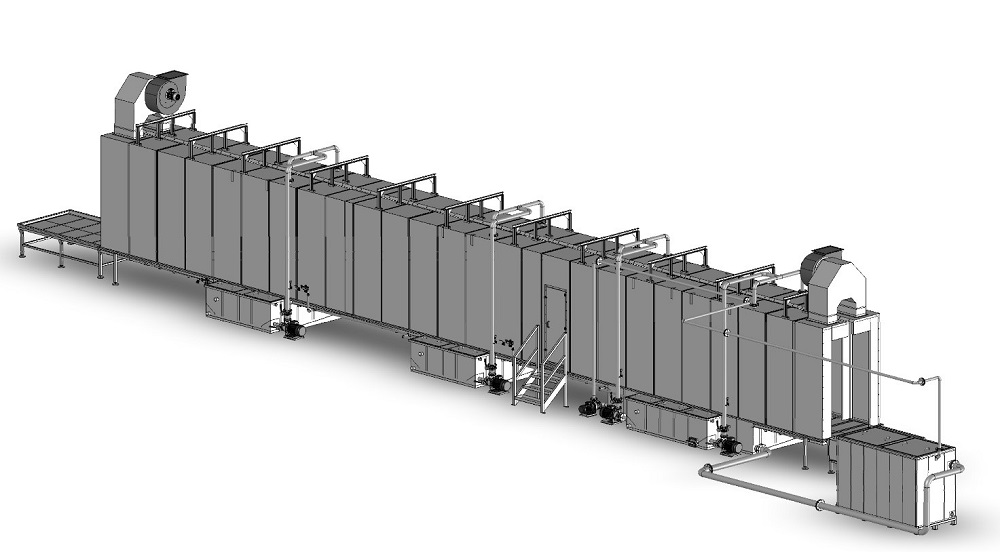
The pretreatment technologies proposed by Verona Impianti
There are different types of systems available on the market for the pretreatment of metal parts. The choice of the most suitable technology depends on various factors related to the specific production needs, the degree of automation of the process and the characteristics of the products to be treated.
Thanks to its solid experience, Verona Impianti 2002 offers a range of solutions aimed to respond to every single specific need.
Pretreatment tunnel
The pretreatment tunnel, also commonly called washing or degreasing tunnel, represents an ideal solution for preparing the products for the subsequent processing phases, in particular painting.
Verona Impianti 2002 designs, builds and installs pretreatment tunnels suitable for any type of metallic material, such as iron, steel and aluminium.
These pretreatment tunnels are built in multiples stages, specifically designed to ensure perfectly clean surfaces ready for powder or liquid painting. Each system is customized according to the customer’s needs, with a careful configuration of the number of stages and the type of treatment desired for the various pieces. During the design process of our tunnels, we also pay special attention to energy efficiency, reliability performance, and to the reduction of energy and water waste.
Cleaning booths
Verona Impianti 2002 also produces cleaning booths, that is, boxes inside which the pieces are cleaned manually to ensure optimal adhesion of the paint in the subsequent phases. Once the component has been inserted into the booth, the operator can proceed with washing using a detergent solution, applied via a pressure washer.
The cleaning booths are distinguished by their ease of use and maintenance. They are particularly suitable for contexts in which it is necessary to contain investments costs, as there are no high production requirements, or when the components to be cleaned are large, making washing in a traditional chemical spray pretreatment tunnel impractical.
Cleaning chambers
Cleaning chambers designed and built by Verona Impianti represent an advanced evolution compared to cleaning booths, offering a highly automated cleaning process of the components before the application of powder or liquid paints. Inside the chambers, the pieces are surrounded by jets of water generated by nozzles positioned laterally, at the top and bottom, ensuring uniform and effective cleaning. An additional option includes the oscillating movement of the components, designed to further enhance the cleaning action.
The cleaning chambers can operate in up to three distinct stages, depending on the level of finish required. A typical treatment cycle begins with a phosphor-degreasing phase, followed by a first rinse with mains water and finally a second rinse with mains water. A tilting system conveys the sprayed solution to the collection tank, from which it is recirculated to the nozzles, optimising water consumption. Verona Impianti’s cleaning chambers are designed to minimise the transfer of solution or water between the various phases, improving the quality of the washing and extending the intervals between bath replacements, ensuring a more efficient and sustainable process.
Verona Impianti: your partner for pretreatment systems
Verona Impianti is specialized in the design and production of custom-made pretreatment tunnels, cleaning chambers and booths, designed to meet the specific needs of each customer.
Thanks to our many years of experience, we create innovative and high-performance systems, capable of optimally managing each phase of pretreatment, ensuring top quality results.
Our pretreatment systems are designed to ensure maximum efficiency and reliability. Whether it is metals, plastics or other materials, each system is designed to guarantee optimal surface preparation, ensuring perfect adhesion of the coating and greater durability of the finished product.
In addition to system design, Verona Impianti offers a complete service that ranges from initial consultancy to implementation
and after sales assistance, ensuring that each project meets the highest standards of quality and sustainability.
Thanks to our pretreatment systems, we can ensure that each stage of the process is carried out precisely and efficiently, minimizing waste and maximizing results. If you want to achieve a superior quality finish and improve the efficiency of your production, Verona Impianti is the ideal partner to rely on.
To find out how we can improve your surface treatment processes, contact us today!